Developed a Profitability Dashboard
I was honored with an award for conducting in-depth analysis of the sales performance over the last five years in the LATAM & MEA regions, leading to the creation of a profitability dashboard. Additionally,
I thoroughly examined the sales data of Yokohama brands, including segments, sub-segments, categories, customers, and patterns, while analyzing key parameters such as revenue, tonnage, EBITDA, and CAGR growth. This analysis highlighted top performers and areas requiring focused attention, earning me the award.
AWARD OF EXCELLENCE
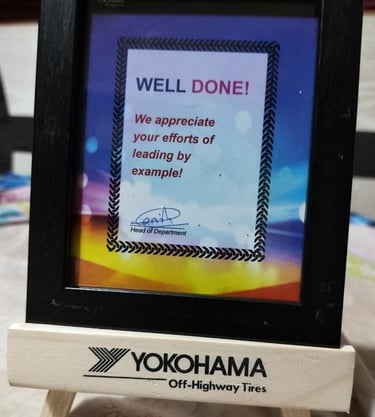
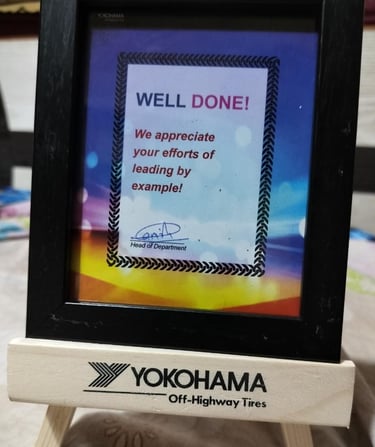
CERTIFICATE OF EXCELLENCE
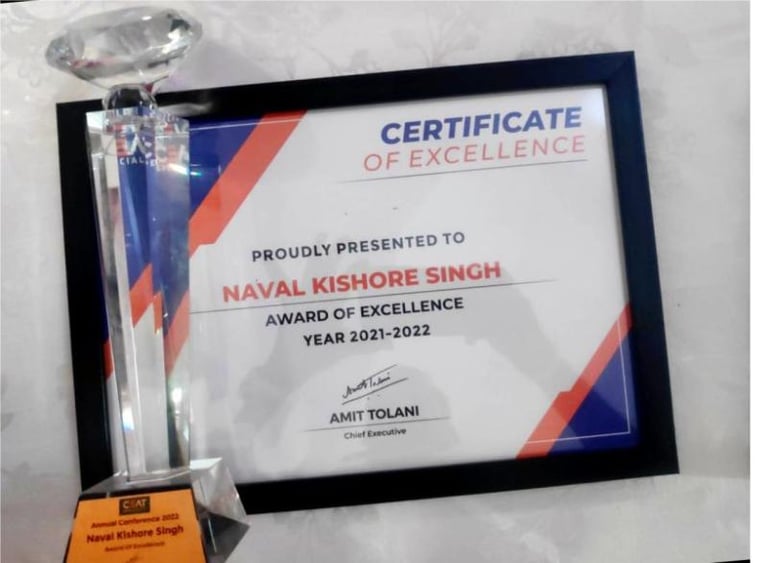
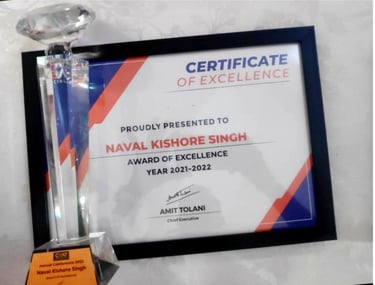
Onboarded Global OEM - Export Market
I led the onboarding of AGCO, a global OEM, to CEAT Specialty, managing a 7-day audit across departments like R&D, Supply Chain, Operations, Strategy & Marketing, and Customer Service. I prepared reports, understood customer tire needs and test results, managed audit findings, and facilitated tire testing for smooth progress.
My role involved driving the process from planning to execution, ensuring alignment between AGCO's needs and CEAT Specialty's capabilities, cementing a successful partnership between the two entities.
Increased OEM Ratings & CSS Score
As Assistant Manager of Customer Quality at CEAT, I handled important clients from various OEMs, dealing with their complaints, services, and audits. I also provided them with necessary support for their business needs. To improve our service, I worked on making the process faster for settling claims.
I also looked at sales and claims data whenever needed to understand our customers better. Additionally, I kept an eye on the progress of new products being developed and launched. All these efforts paid off as our ratings with OEM suppliers increased, and our customers became more satisfied with our services.
CUSTOMER CENTRICITY AWARD - Runner's Up
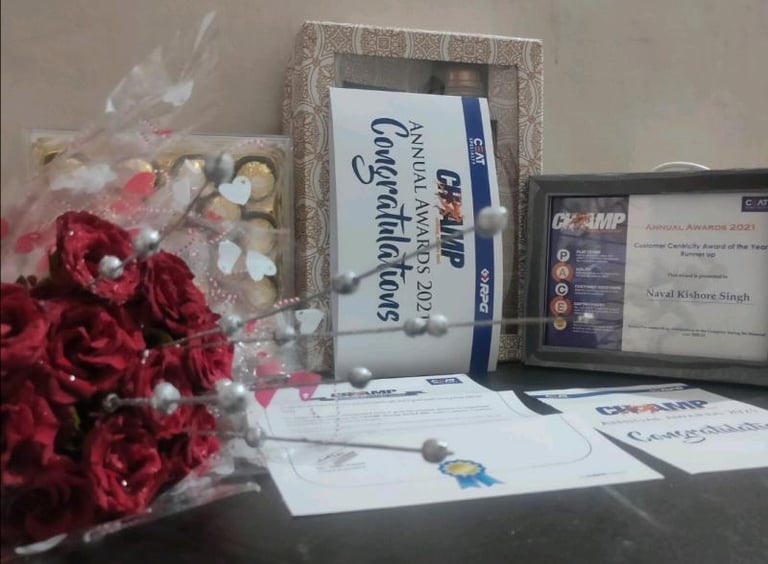
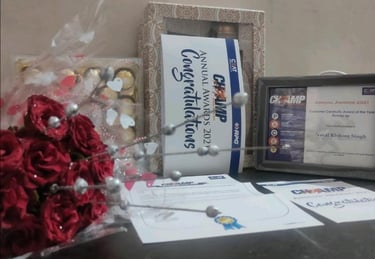
PAR EXCELLENCE - NCQC (Varanasi & Gwalior Chapter)
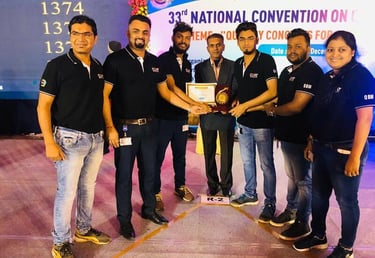
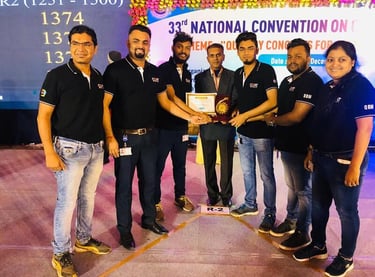
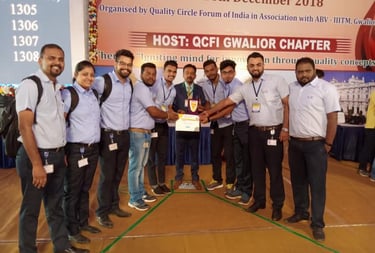
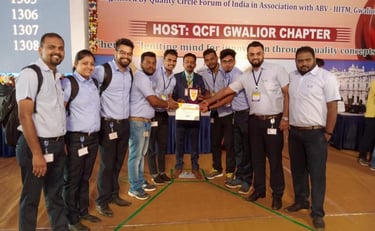
Increased Operation Efficiency of Tire Building
I earned the first prize (Par Excellence) nationally for leading a detailed improvement project targeting the operational efficiency of tire manufacturing. This initiative involved multifaceted enhancements spanning production planning, machine downtime reduction, and tire cycle time minimization.
Key strategies encompassed the implementation of Single-Minute Exchange of Die (SMED) projects for streamlined changeovers, meticulous mapping of machine specifications to optimize performance, and the adoption of digital solutions for enhanced production planning.
These concerted efforts culminated in substantial operational efficiency gains, cementing our standing as industry leaders and earning us esteemed recognition at the national level.
Eliminated Ply Stuck Up Phenomenon
I led a project targeting the elimination of plystuck, a critical issue in our manufacturing process. Forming a quality circle team, we identified the problem, collected data, and conducted thorough analysis.
Utilizing Ishikawa diagrams, we brainstormed solutions, which underwent rigorous testing before implementation. Once validated, we standardized the improvements and updated documents like SOPs and Control Plans.
This initiative resulted in an estimated annual saving of around 4 Lakhs while ensuring sustained quality enhancements. Our systematic approach not only resolved the plystuck issue but also showcased the impact of collaborative problem-solving on operational efficiency and cost reduction.
Gold Award - CCQC (Mumbai Chapter)
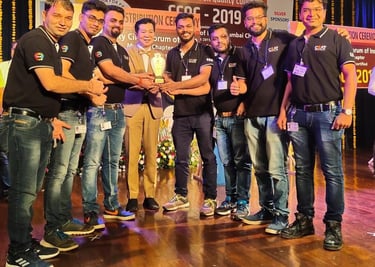
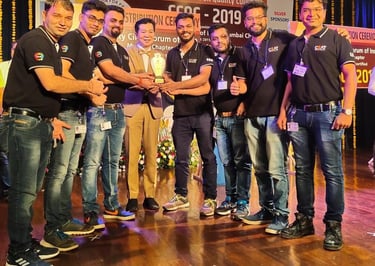
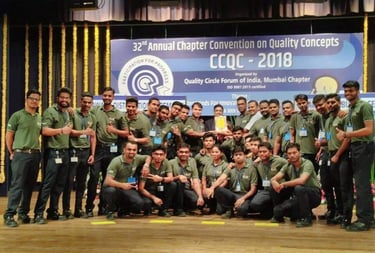
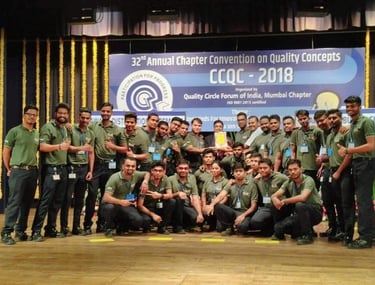